【返回
技术文章列表】 |
油脂化工厂系统化学清洗研究与应用 |
左理胜 姜建平 |
(广州垦源化工科技有限公司) |
摘要:文章介绍了油脂化工厂脱臭、综合系统的结垢情况及系统化学清洗的清洗配方、工艺,对清洗机理进行探讨,并介绍了在巴陵油脂公司的应用情况。
关键词:油脂 系统清洗 化学清洗 结垢
|
The Research And
Applied On The Systematic Chemical Cleaning of
Fat Chemical Plant |
Zuo Lisheng Jiang Jianpin |
Abstract: This
paper introduces the fouling in Fat Chemical
Plants,such as the systems of deodorant and
complex. It introduces the cleaning formulation
and process of system chemical cleaning. The
cleaning theory is discussed, Applied situation
in Baling Fat Chemical Co. Ltd is introduced,
too.
Key words: Fats and
oils Systematic cleaning Chemical cleaning Scale |
脱臭系统和综合系统是油脂化工厂油品精制的主要装置,由于系统运行温度较高,容易产生油焦堵塞管道、降低传热效率严重影响正常生产,传统的清洗方法是停工后打开设备人工清扫或高压水射流清洗【1】,这些方法都存在着清洗时间长、除垢效果不均匀等缺点,特别是对于螺旋板换热器和系统管线等设备清洗效果更差。为了解决这一问题我们根据装置的实际情况,研究了脱臭、综合系统清洗的清洗配方和清洗工艺,并对巴陵油脂公司脱臭系统和综合系统进行多次成功的系统清洗,取得了很好的清洗效果:除油率大于98%,除焦垢率大于95%,腐蚀率小于0.4g/㎡.h;清洗后脱臭系统流量从2m3/h提高到10m3/h以上,有效地提高了装置的生产能力,降低能耗,有较好的经济效益和推广应用前景。本文以巴陵油脂公司脱臭系统和综合系统的清洗为例介绍该技术。
1、结垢情况及危害 |
巴陵油脂公司脱臭系统和综合系统主要有容器、换热器、塔及管线等设备,经过多年的运行后,设备表面结垢严重,特别是螺旋板换热器E702、E703表面由于运行温度较高,堵塞严重,系统流量流量从10m3/h逐步下降到2m3/h,已经影响正常生产。由于系统内部介质及工艺条件不同,设备表面沉积的污垢差别较大,具体情况见表一。
|
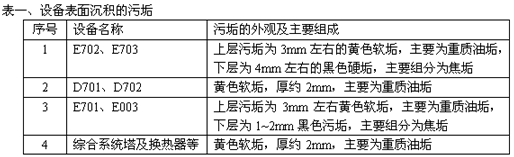 |
这些污垢的存在将主要带来以下问题:一、影响产品的质量,由于污垢粘度大、颜色深,进入成品中影响产品的品质;二、降低传热效率:由于污垢的传热系数小,热阻大,使得设备的传热效果降低,导致物料温度不能满足工艺要求;三、大量污垢沉积在设备及管线表面,导致管径变小,阻力增大,严重影响正常生产。
2、清洗配方及工艺机理
2.1清洗配方
从表一可以看出,不同系统内部污垢差别较大,为此我们针对两个不同的系统研究清洗配方,由于污垢主要以重质油垢和油焦污垢为主,我们选取了SL-1油分散剂、乳化剂TX、渗透剂及三种助剂进行试验,具体情况如下:
考虑成本因素及操作方便,结合我们的清洗经验,各组分的实验浓度如表二。
|
 |
实验结果结果如下:
|
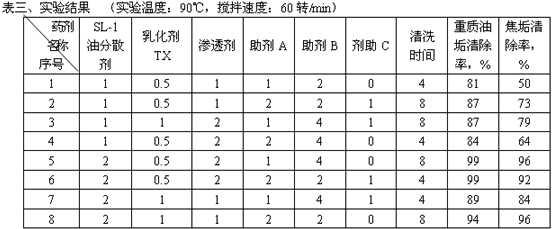 |
从上表可以看出:5#配方清除重质油垢和焦垢的效果均十分理想。因此清洗配方为:2%SL-1油分散剂+0.5%乳化剂TX+2%渗透剂+2%助剂A+4%助剂B。
|
2.2清洗工艺
根据现场情况决定采用以下工艺流程进行清洗:
图1、脱臭系统清洗流程示意图
图中:1:清洗车,2:清洗泵,3:D701,4:P701,5:E704,6:E703,7:E701,8:E702,9:导热油换热器,10:D702,11:P702。
流程说明:清洗液从清洗车中经过清洗泵打入D701,由P701从D701底部抽出经E704、E703、E701、E702管程通过导热油加热后打入D702,由P702从D702
底部抽出经E702、E701壳层打入D701建立循环。
图2、综合系统清洗流程示意图
图中:1:清洗车,2:清洗泵,3:T011,4:P011,5:E011,6:M011,7:M012,8:P012,9:M013,10:D013,11:P013。
流程说明:清洗液从清洗车中经过清洗泵打入D701,由P701从D701底部抽出经E704、E703、E701、E702管程通过导热油加热后打入D702,由P702从D702底部抽出经E702、E701壳层打入D701建立循环。
3、现场清洗
按照以下步骤进行清洗清洗步骤:
3.1系统注水:向系统内中注水;
3.2根据清洗工艺流程的要求启动系统泵建立循环;
3.3运行10min后检查系统是否泄漏,如果系统有泄漏则进行处理,不泄漏则停泵,将水排放少量;
3.4计量加入清洗药剂到清洗车中,开启清洗泵打入系统内;
3.5按照步骤3.2开始进行清洗,启动加热系统将清洗液加温至90℃以上;
3.6通过人孔观察塔盘的清洗效果,清洗干净后逐层切换;
3.7每隔1~2h取样观察清洗液的粘度,并测定清洗液的表面张力、腐蚀率等指标,清洗液的表面张力基本保持不变时停止清洗;
3.8排放,并用清水冲洗干净。
4、机理探讨
清洗液主要由油分散剂、乳化剂、渗透剂和助剂组成,具有较低的表面张力、较强的渗透能力,清除重质油垢的过程可以分为以下几个阶段,首先是润湿、渗透阶段:由于清洗液具有较低的表面张力,当清洗液与污垢接触后,清洗液与污垢的接触角很小,能迅速润湿污垢并铺展在污垢的表面,活性剂分子的疏水基吸附在污垢表面,而亲水基则溶解在清洗液中,这样表面活性剂分子均匀整齐地排列在污垢的表面,从而使清洗液充分地润湿污垢表面;由于清洗液具有较强的渗透能力,表面活性剂分子能穿过污垢表面的微小间隙进入污垢内部;第二,乳化、分散:当清洗液进入污垢内部后,与之发生反应,形成水包油的乳液,在机械力的作用下脱离污垢本体,分散到清洗液中,达到清除污垢的目的【2】【3】;第三,分解:重质油垢的油焦等物质,由于结焦形成的物质颗粒较大,不容易被乳化分散,加入助剂后,使之分解为分子量较小的颗粒而被乳化分散到清洗液中;第四,冲洗剥离:由于清洗液的流动,使部分污垢从设备表面冲洗剥离下来,使污垢清除干净;第五,混合相的形成:清洗下来的污垢在分散在清洗液中形成混合相随清洗液带走,防止污垢再沉积。
5、清洗效果
为了了解清洗效果,我们测定了清洗液在清洗过程中的固含量、表面张力、油含量、腐蚀率,表四是2001年5月巴陵油脂公司脱臭、综合系统清洗时清洗液的测定结果。
|
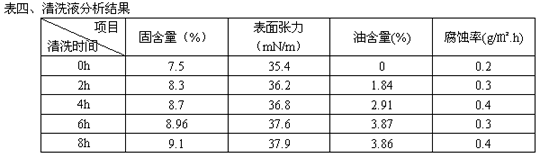 |
从上表可以看出:清洗液的固含量、油含量逐步增加,表面张力逐步升高,6-8小时后基本保持不变,说明清洗基本结束;从腐蚀率测定结果可以看出:清洗液对设备的最大腐蚀率为0.4g/㎡.h,对设备基本无损害。
|
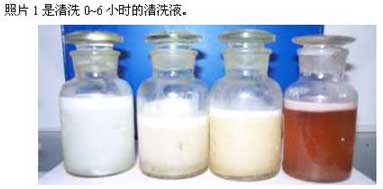 |
照片1、清洗液(从左到有依次为清洗0h、2h、4h、6h的清洗液)
从照片看出:清洗液颜色逐步加深,说明污垢逐步从设备表面脱落溶解、分散在清洗液中。
清洗后打开设备检查,塔盘表面无污垢,基本见金属本色,而螺旋板换热器及管线内可见部分没有污垢存在。清洗后开工系统流量从清洗前的2m3/h提高到10m3/h以上说明换热器及管线基本清洗干净。
6、结论
6.1实践证明,系统化学清洗具有许多优点:一、可以弥补单台设备人工或高压水射流清洗的不足,清洗效果更好;二、实施系统清洗,可以缩短检修时间,不延误工期,同时系统清洗后换热器不需要打开可以节约检修费用。
6.2研究的清洗配方具有清洗效果好、对设备损害较少、对环境无污染等优点。
6.3采用研究的清洗方法能有效地提高了装置的生产能力,降低能耗,有较好的经济效益和推广应用前景。
7、参考文献
【1】吕文柱等,油脂化工厂蒸发器的高压水射流清洗工艺研究[J].中国油脂,1999,24(1):20-21
【2】 E.H.Luccassen-Reynders(美)著,朱步瑶等译.《表面活性剂作用的物理化学》[M],轻工业出版社,1988.261-302
【3】梁治齐,张宝旭编.《清洗技术》[M],轻工业出版社,1998.90-124 |
|